COMPONENTS
FRASCA Systems
Your content goes here. Edit or remove this text inline or in the module Content settings. You can also style every aspect of this content in the module Design settings and even apply custom CSS to this text in the module Advanced settings.
Cockpits
Instrument Panel
Flight Test Modeling
Avionics
Control Systems
Visual Systems
Composites
Structural
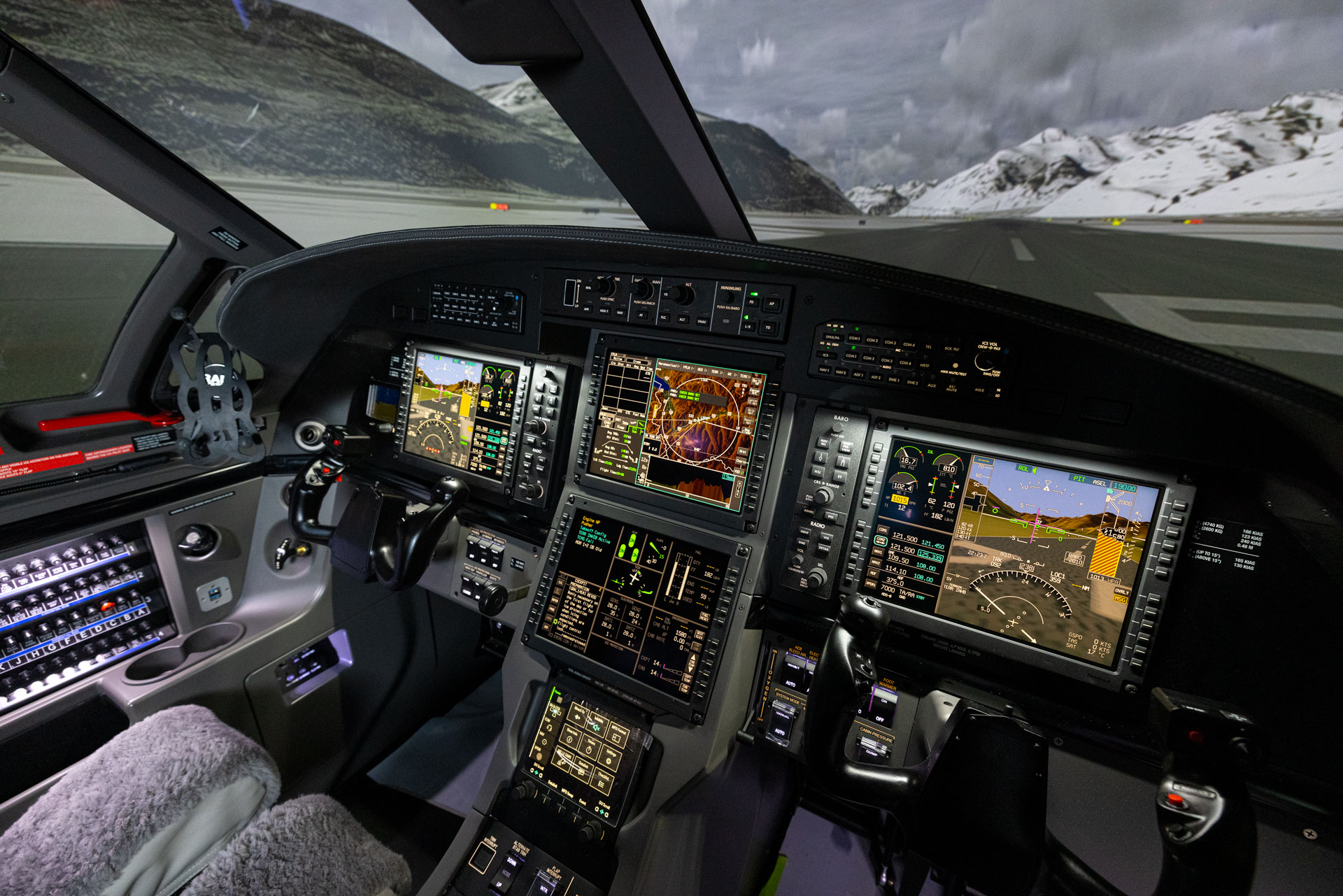
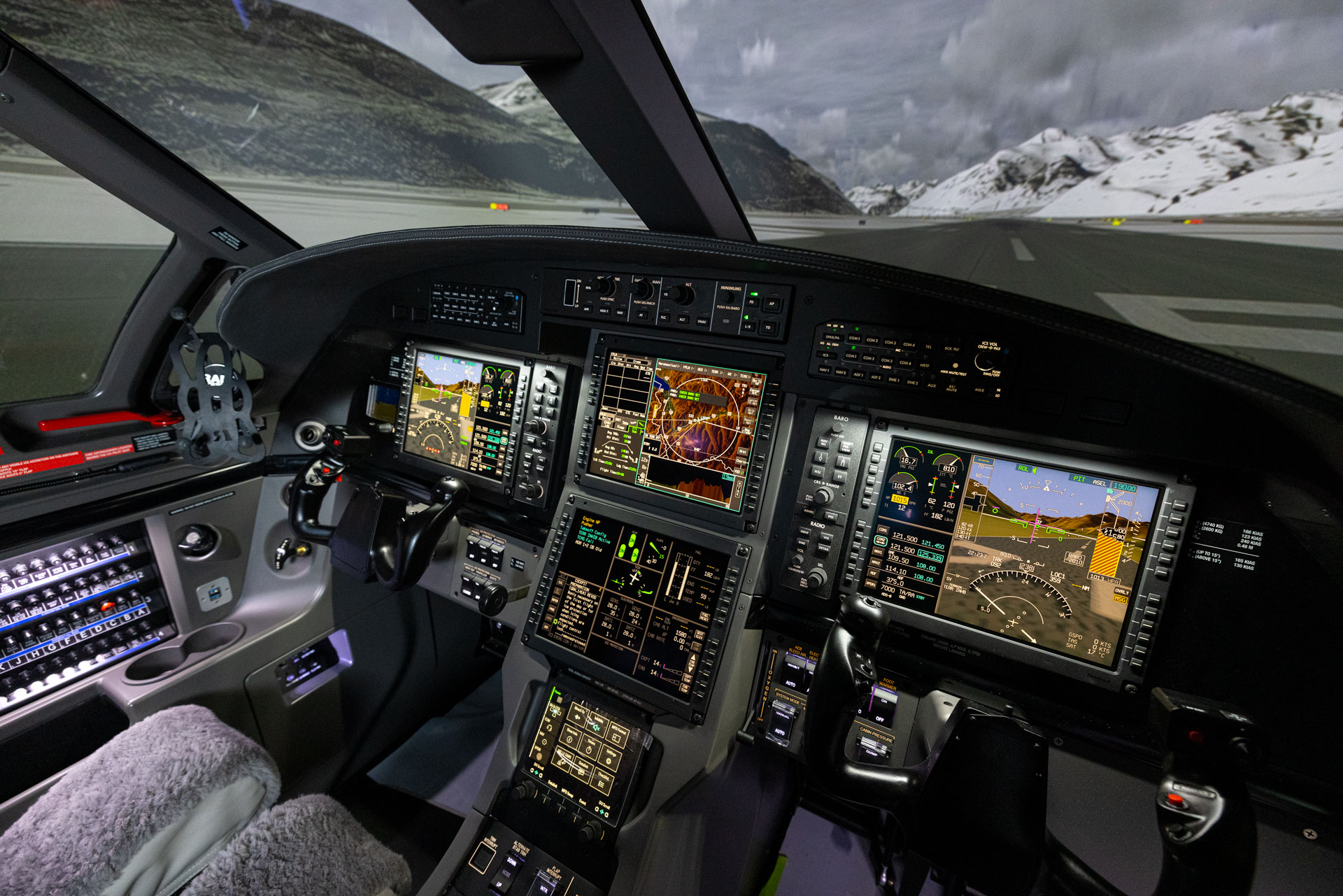
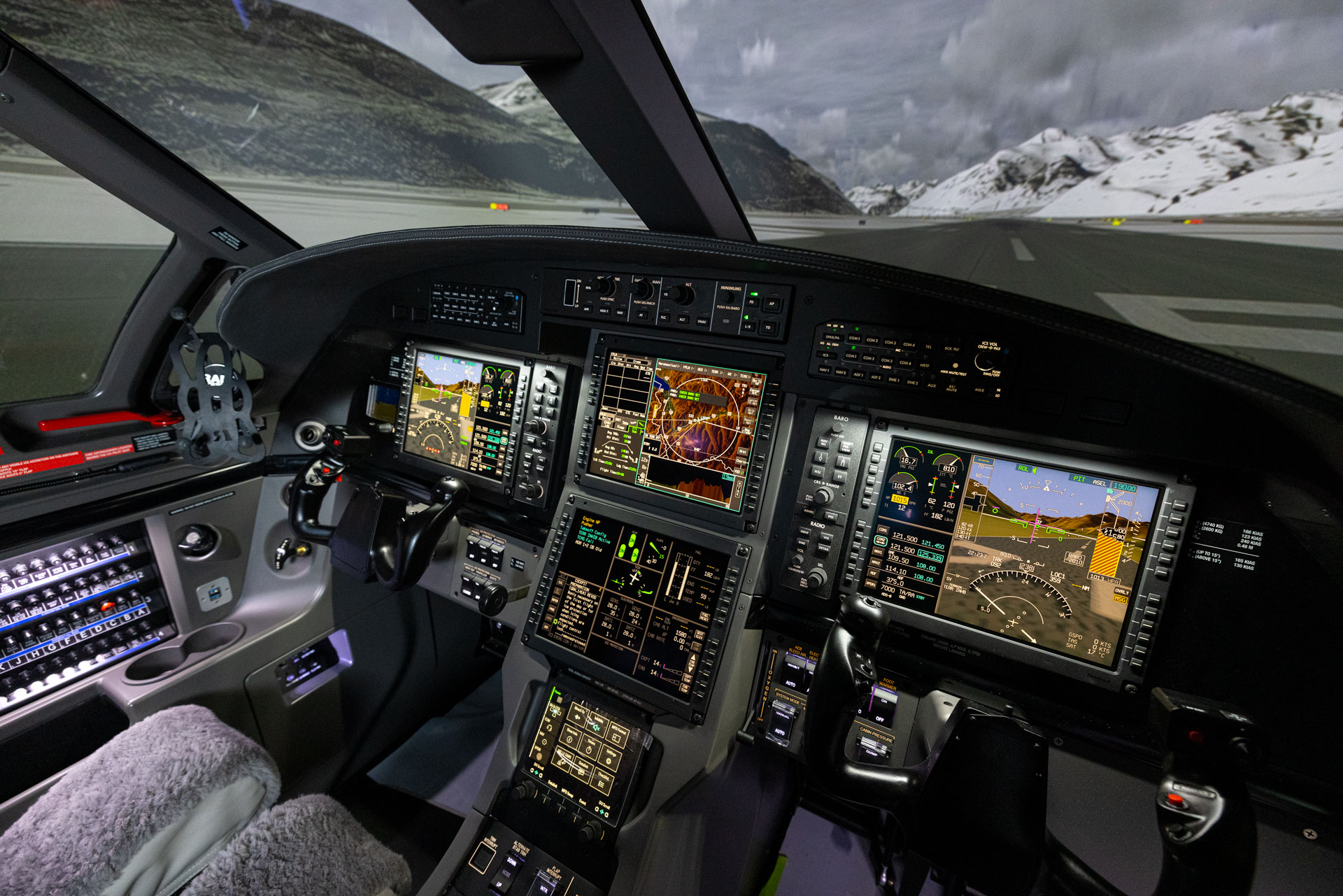
Cockpits
Frasca produces realistic high quality simulator cockpits. These can range in complexity from bare cockpit shells to fully populated cockpit assemblies inclusive of control loading systems, instruments and IO systems. Each cockpit is designed to the buyer’s specific requirements. These replica cockpits carry the advantages of being designed and constructed to withstand the physical strains encountered in flight simulators.
Instruments & Panels
Frasca designs and manufactures simulated aircraft instruments and control panels. Instruments include both mechanical and electronic displays. When appropriate, designs can include electronic interfaces and firmware to enable interfaces to a wide range of protocols.
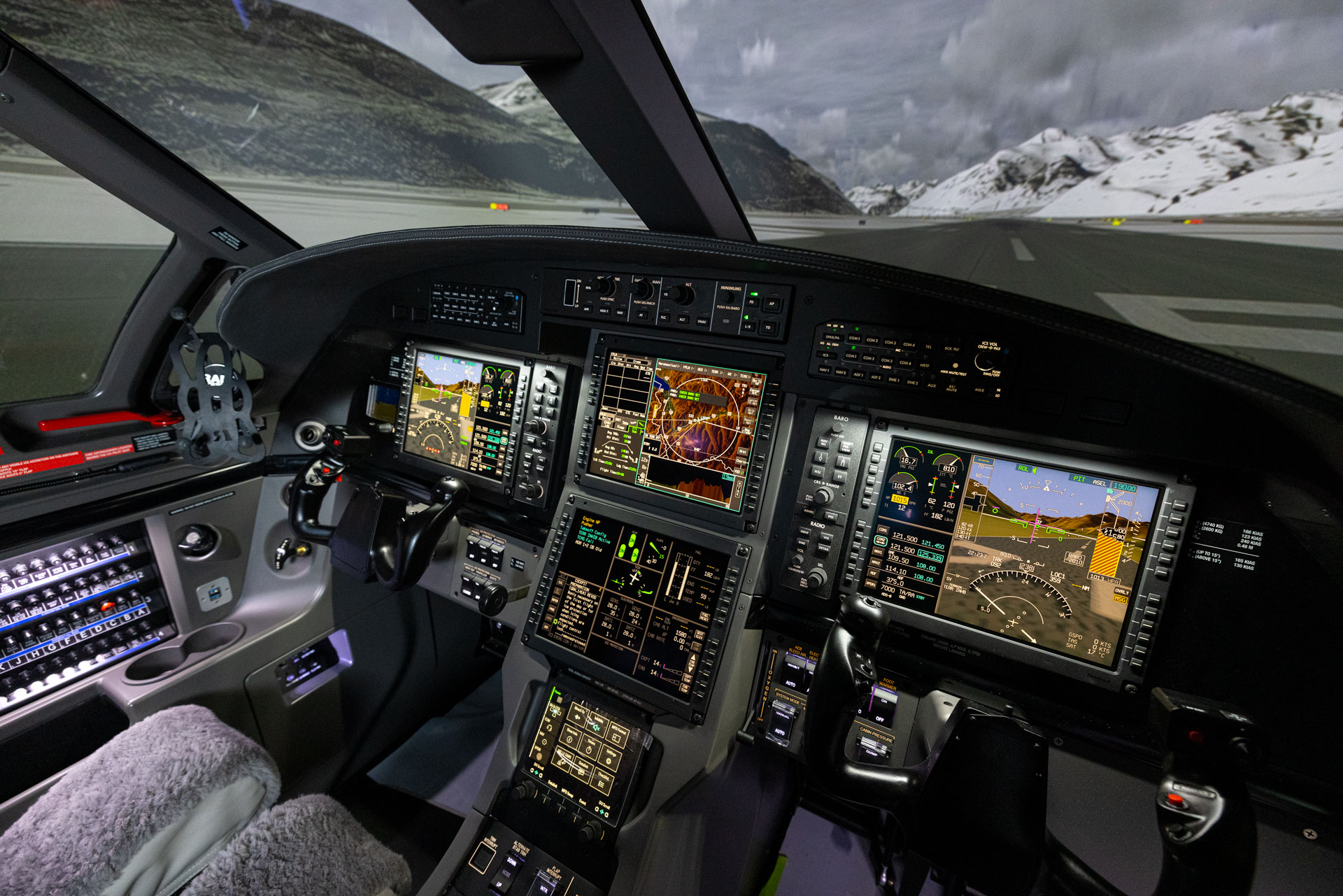
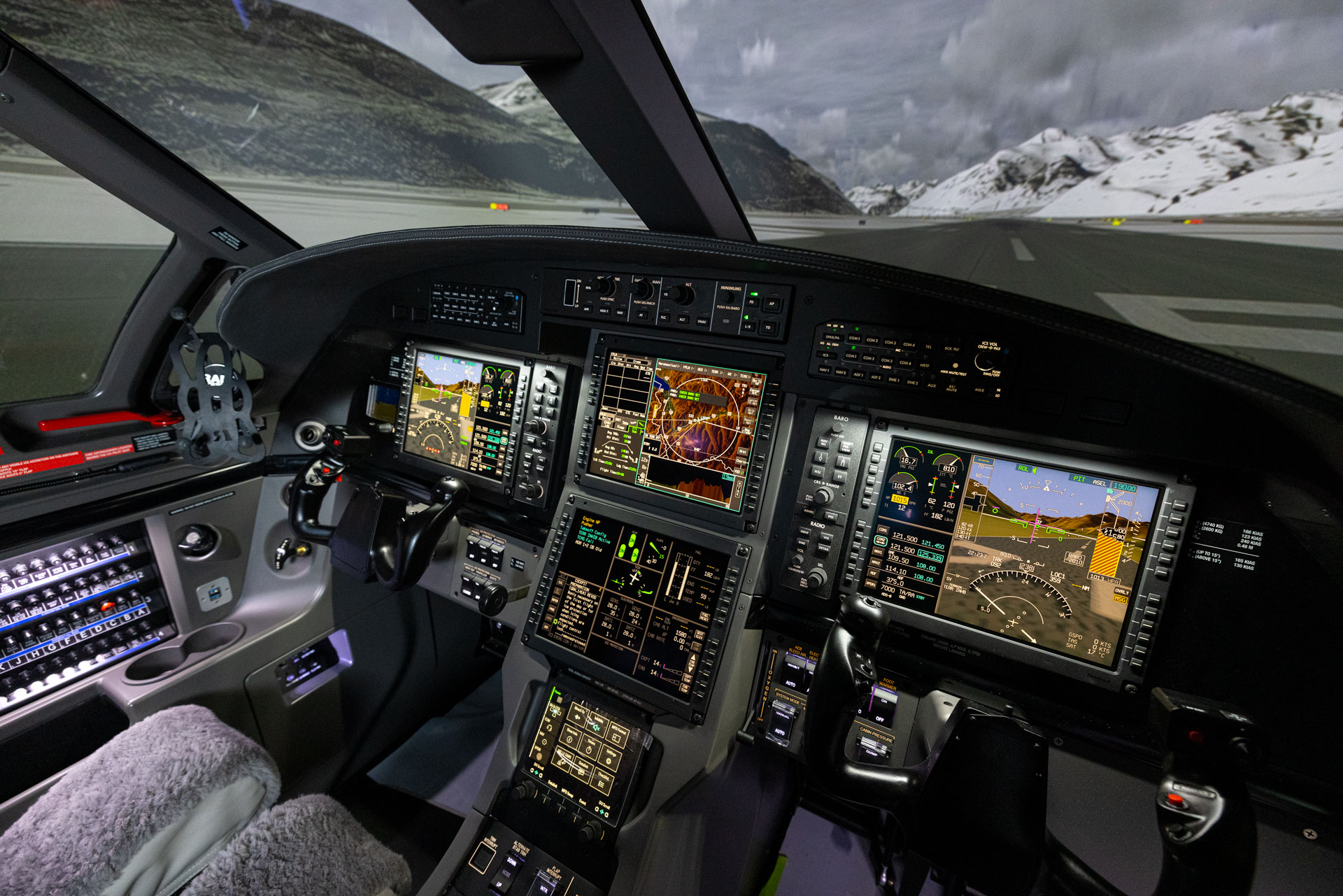
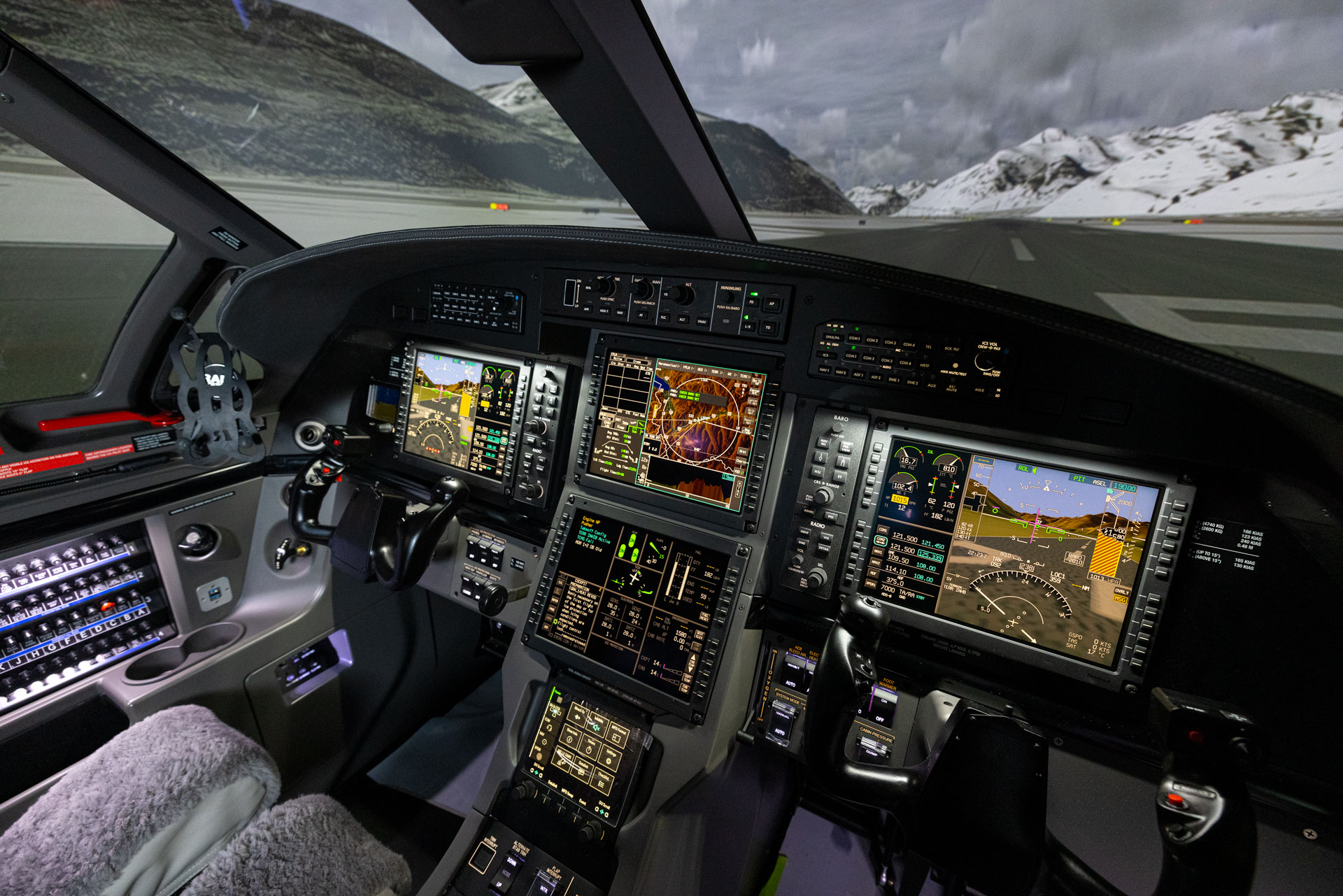
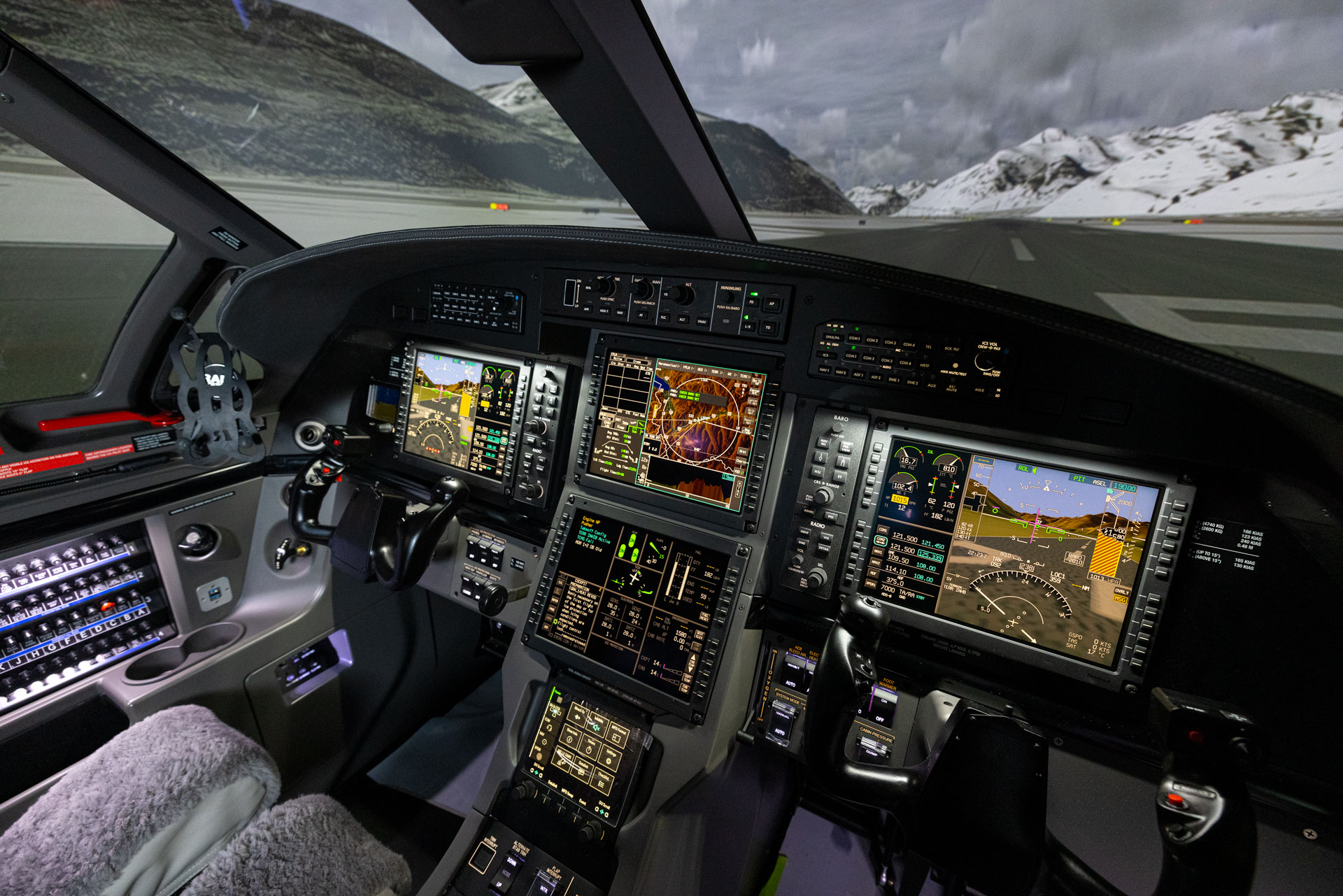
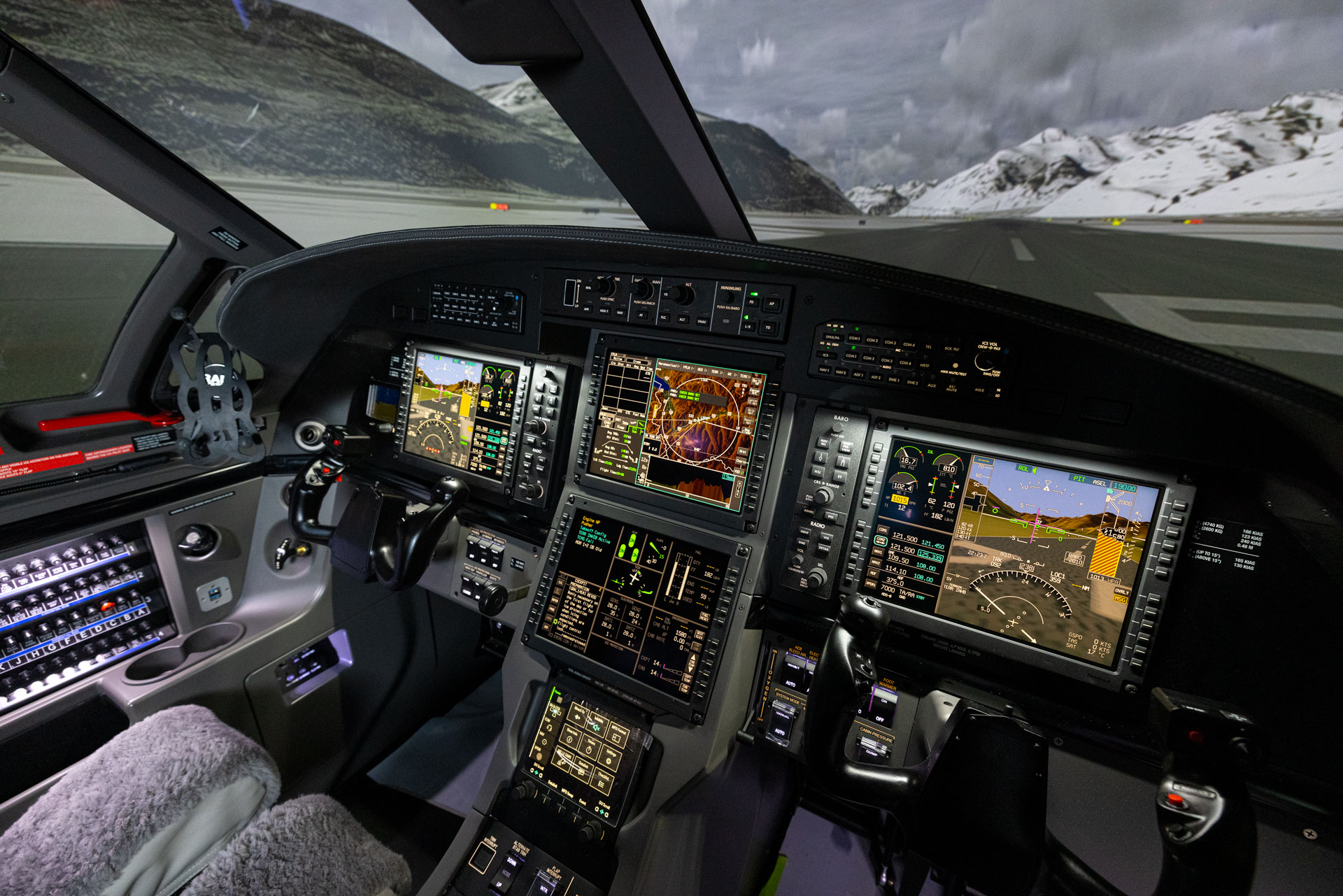
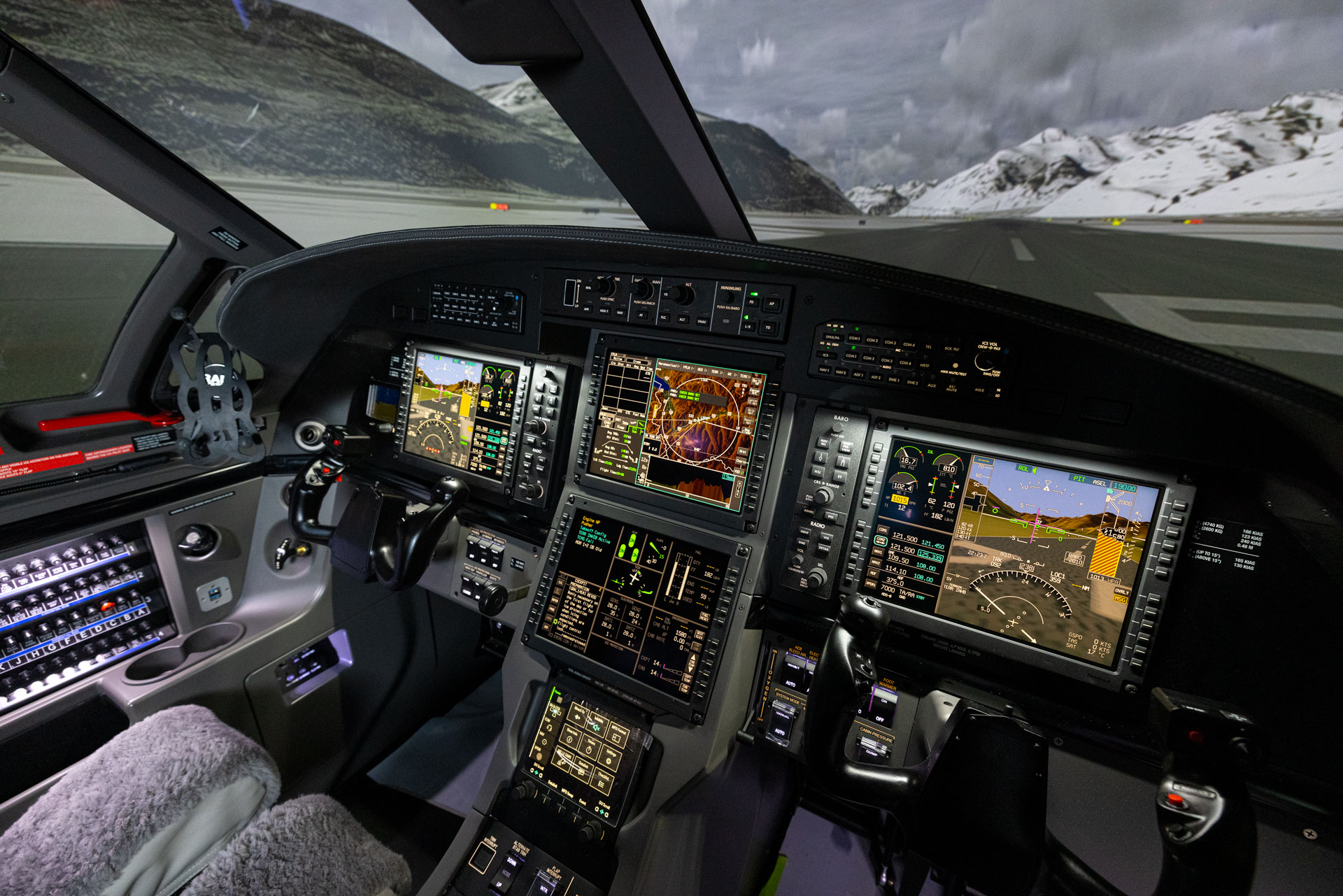
Avionics
Frasca has developed interfaces for many of today’s most popular avionics. These include Garmin, Avidyne, Aspen, Rockwell Collins, Universal and more.
Visual Systems
Frasca’s TruVision™ Global puts you in the middle of a highly detailed world with custom options for satellite/aerial imagery, terrain mapping, and modeled details. Our Image Generator uses the best available COTS PC hardware and FRASCA’s TruVision™ Global software. Display systems are available in single-channel direct view and projected configurations, as well as wrap-around multi-channel configurations with large horizontal and vertical fields of view. Worldwide depiction of over 10,000 runways, terrain, world-wide coastlines, and fully variable time of day are all standard features. TruVision™ Global adds incredible realism and training value to your simulator.
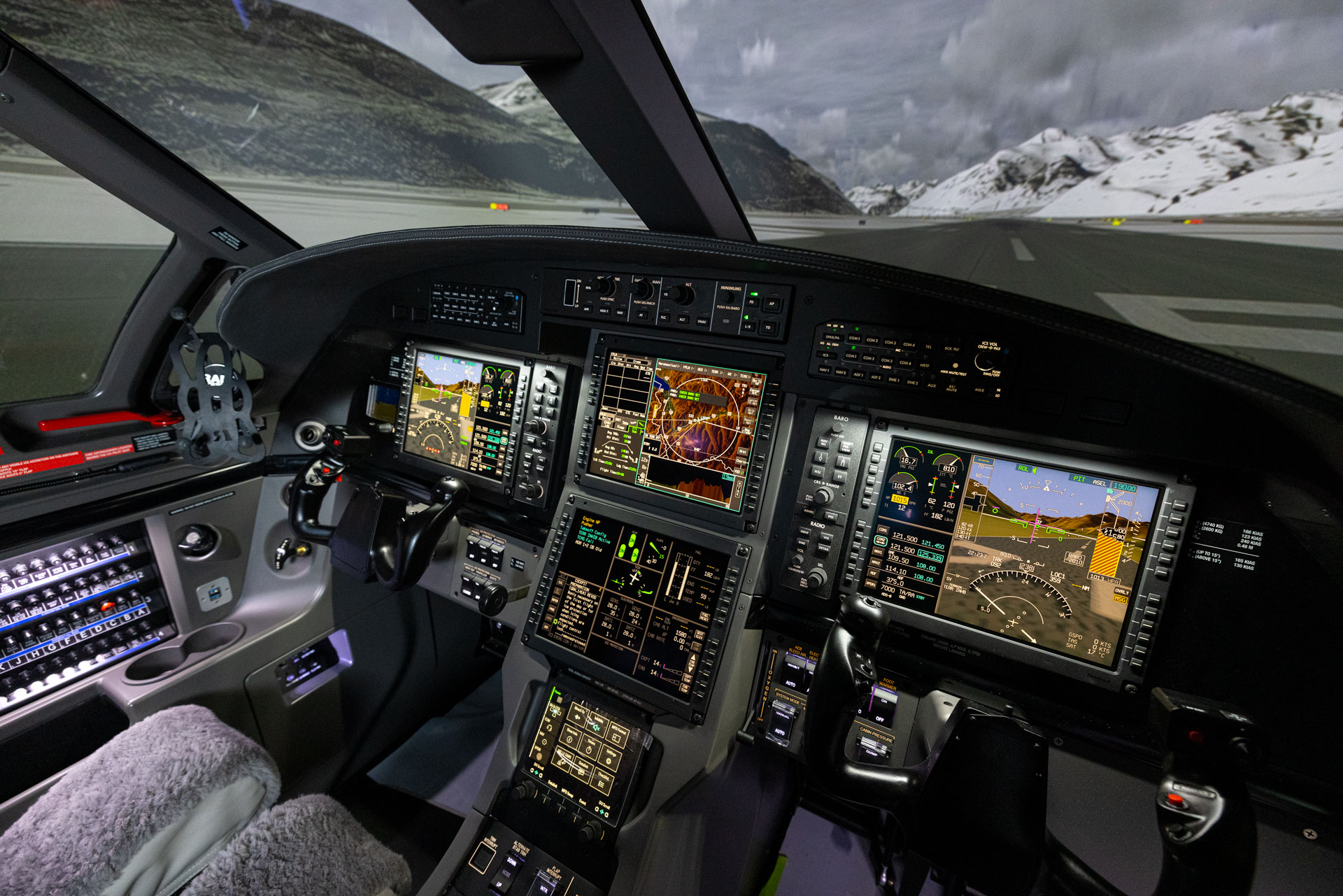
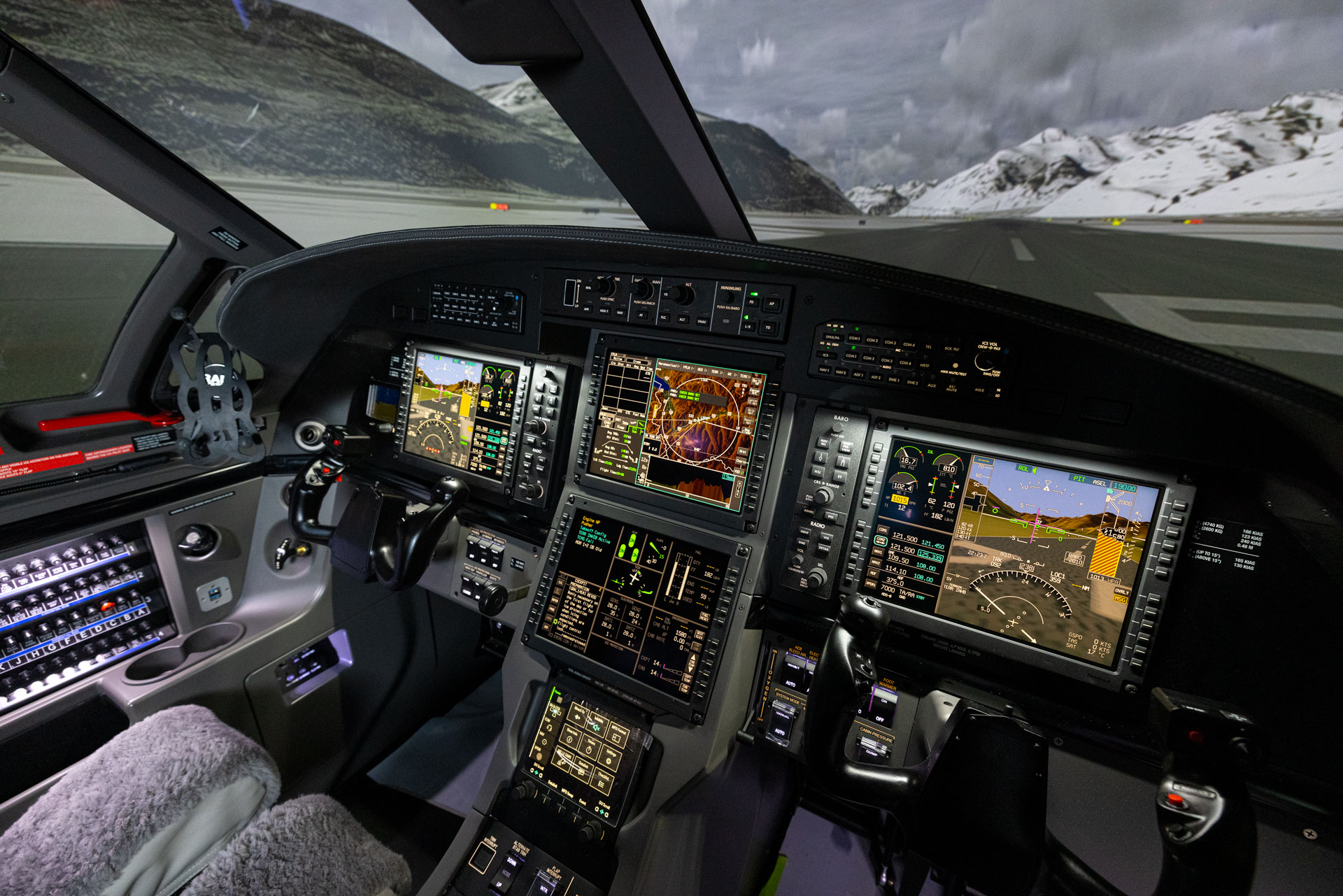
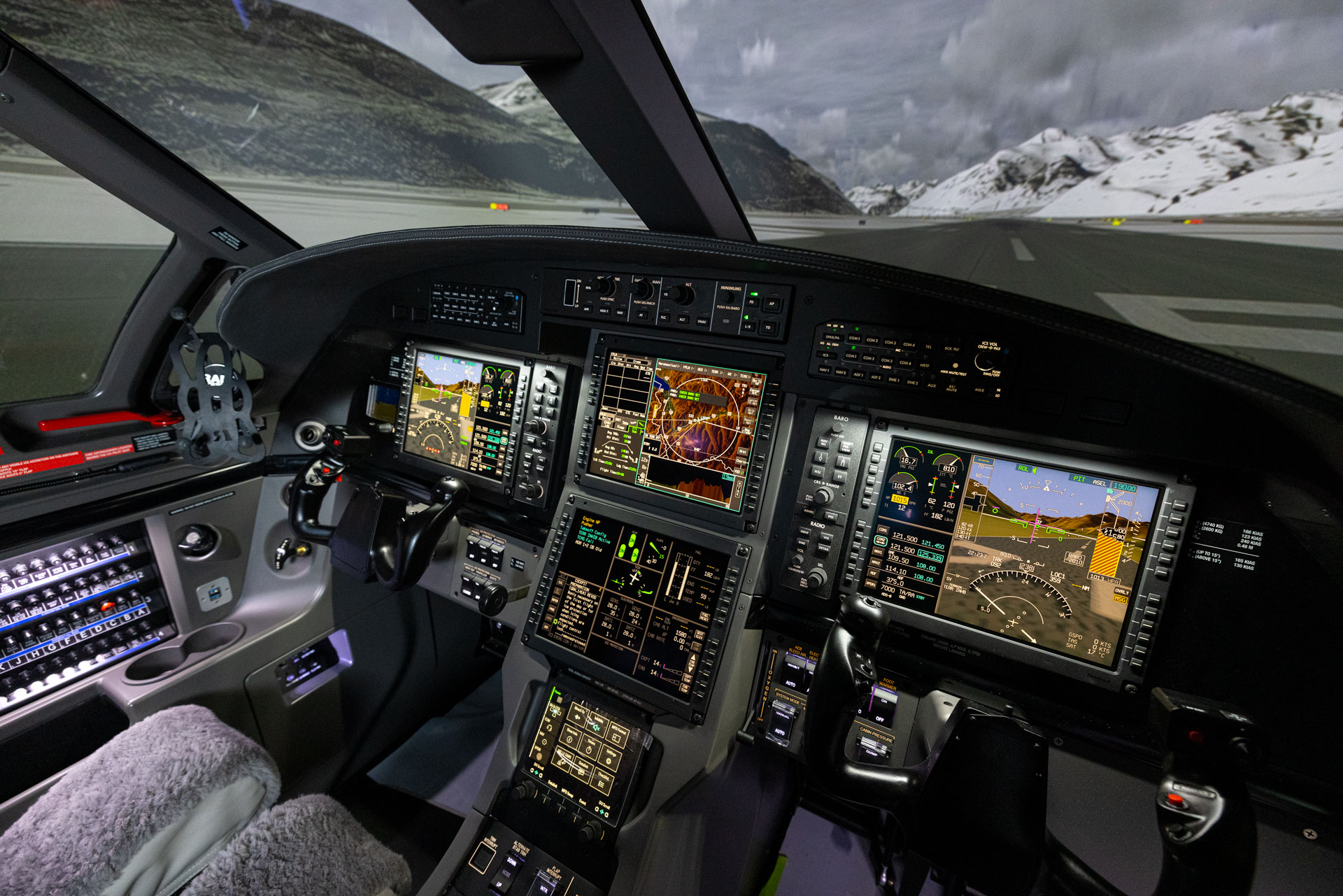
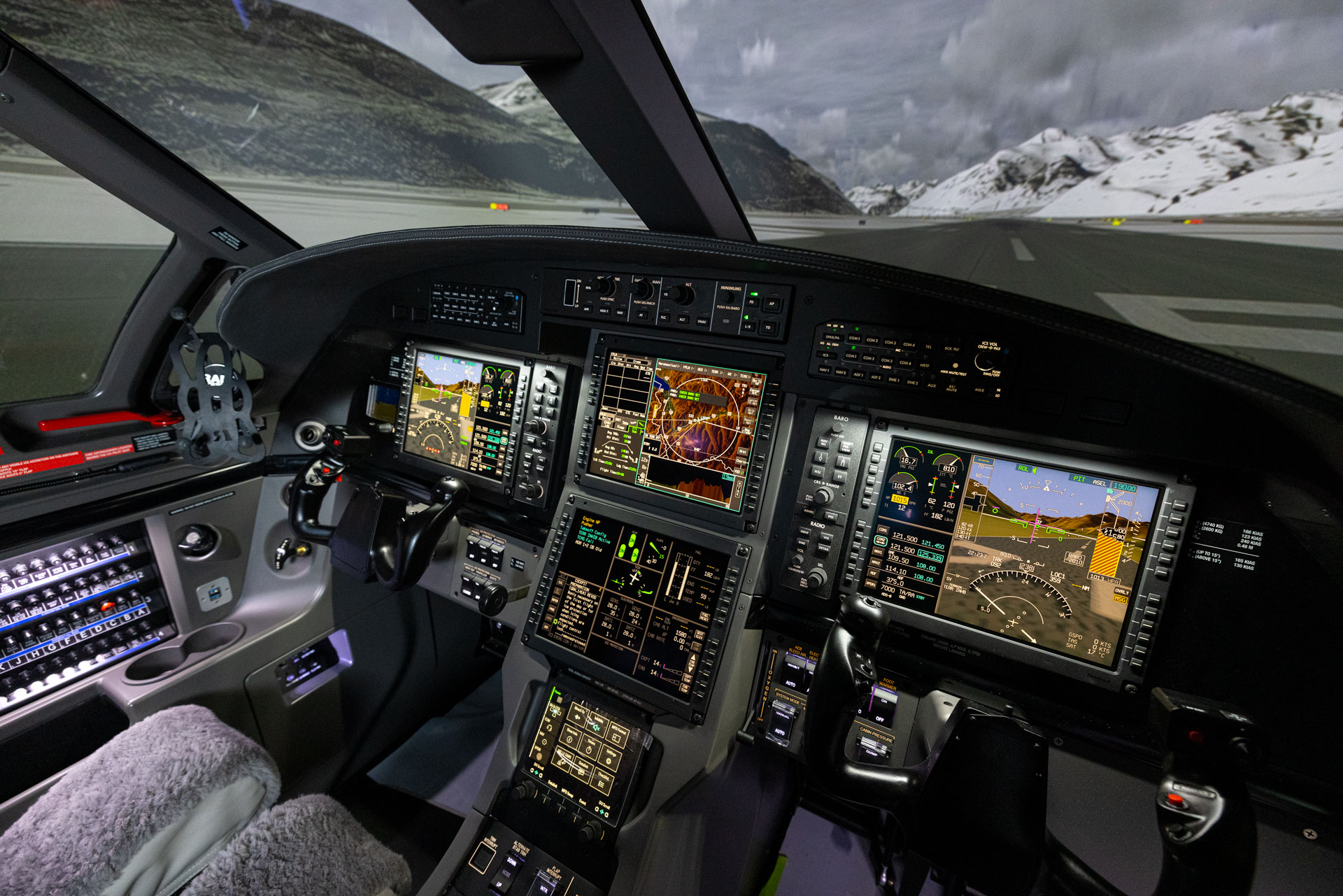
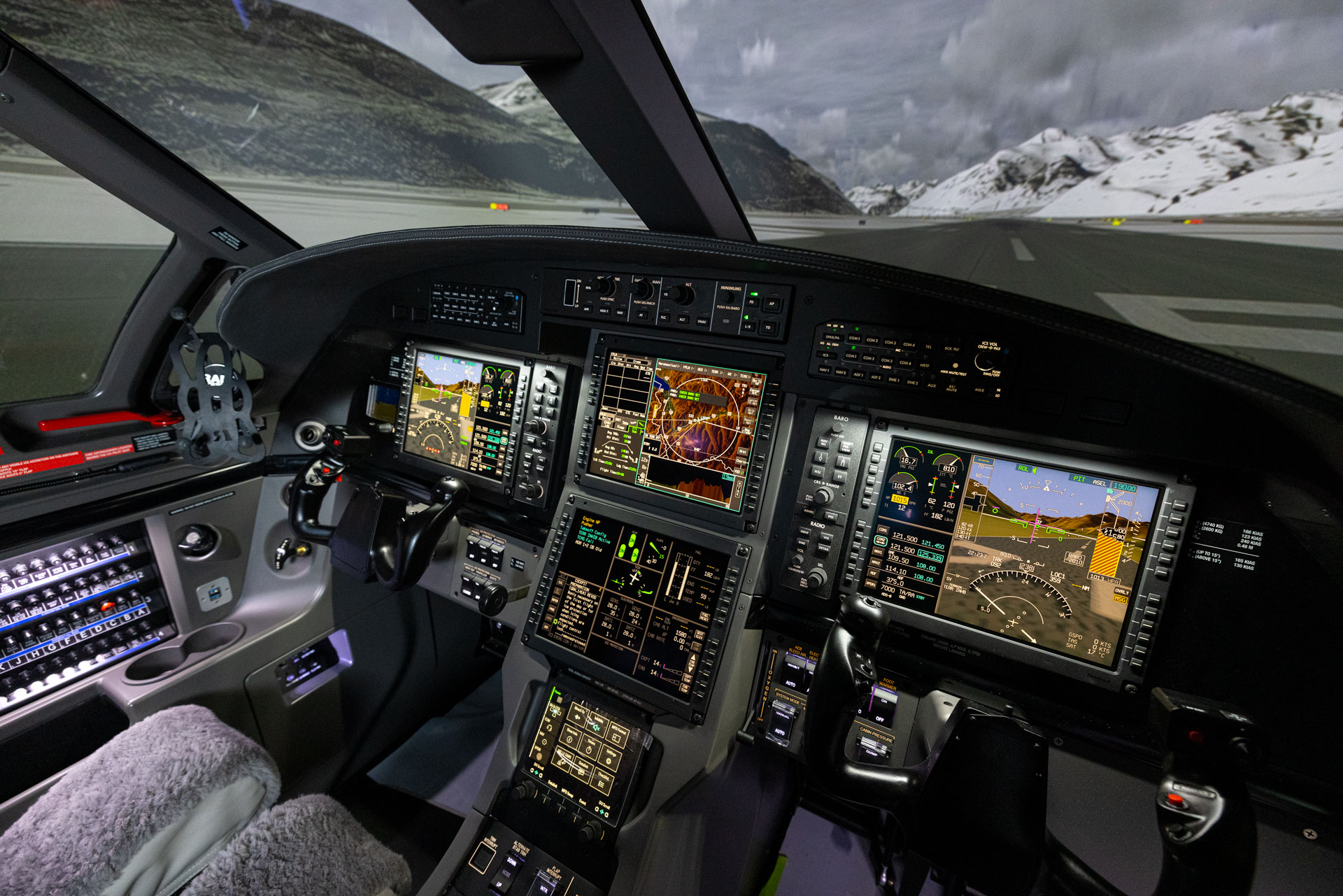
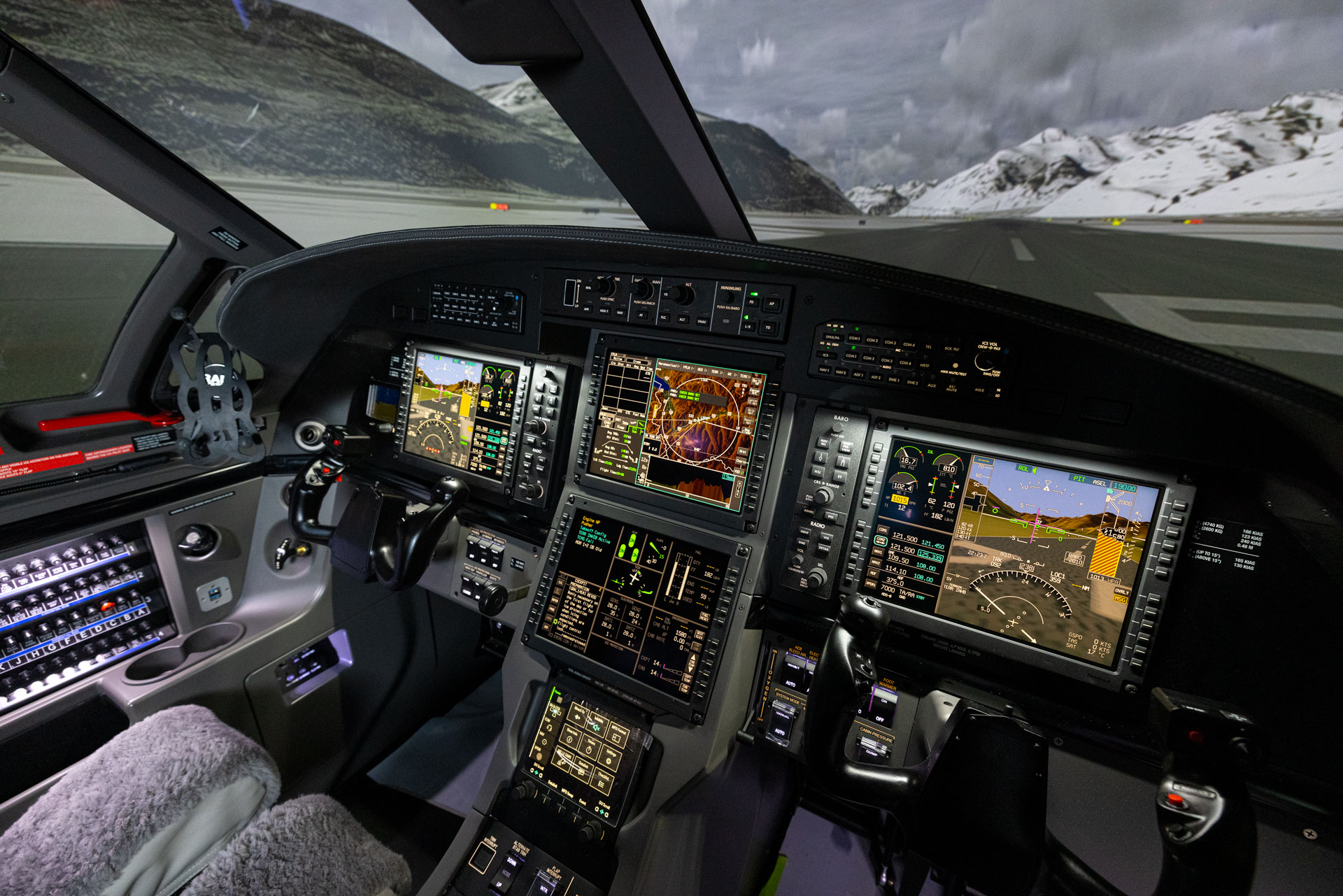
Composites
Frasca designs and fabricates patterns and molds for composite parts. These include cockpit shells, visual display screens, cosmetic covers, flight test instrumentation fixtures, etc. Frasca then uses the molds to produce finished composite parts for use in flight simulators.
Structual Components
Structural components including cockpit base frames, motion flying platforms, boarding ramps, and composite honeycomb cab assemblies are designed and manufactured by Frasca. Designs are validated using Finite Element Analysis. Welding is certificated in accordance with the American Welding Society, AWS.
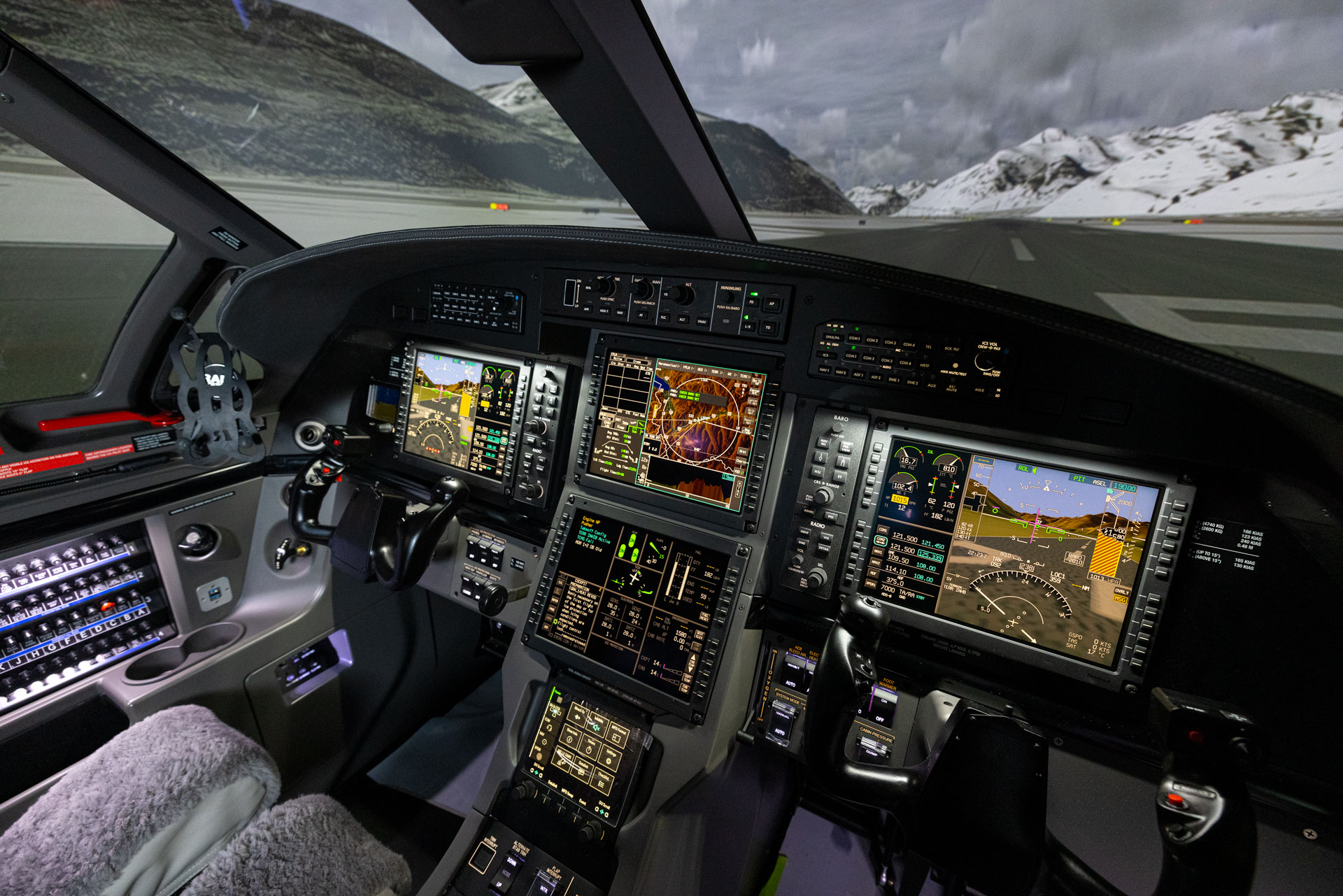
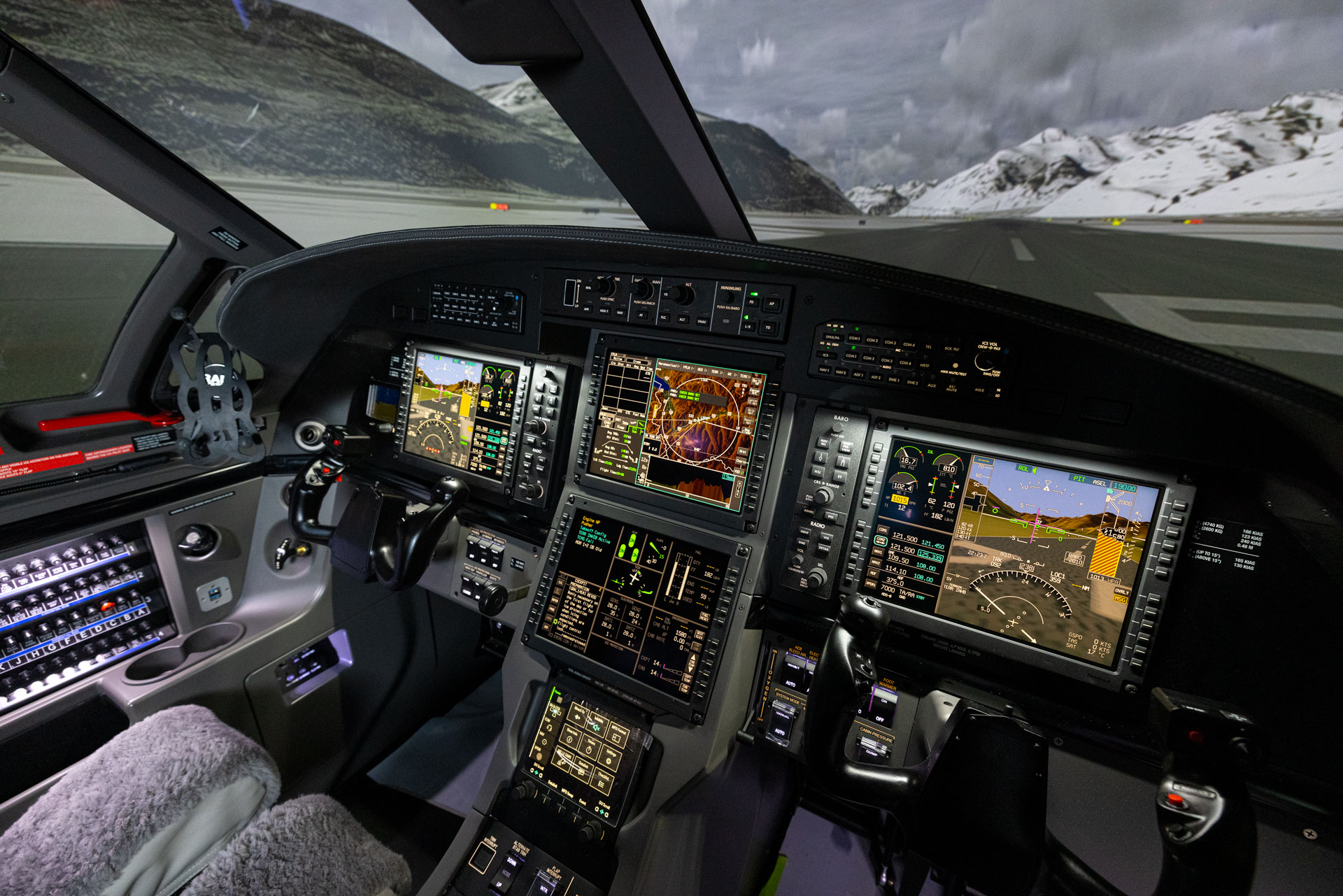
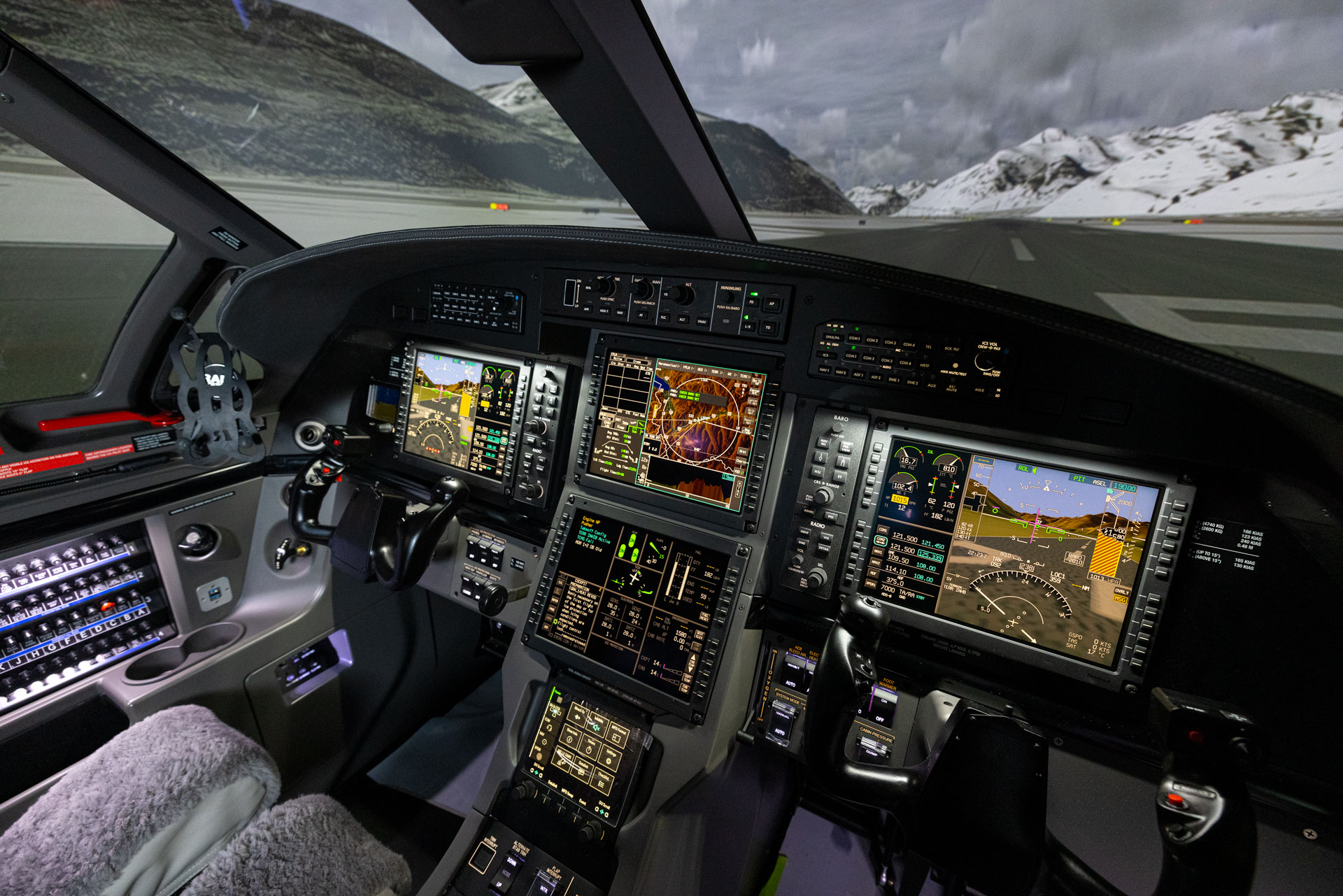
STAY CONNECTED
Stay up to date with all things FRASCA. Sign up for our Quarterly eSimuLetter.