What does it take to make great, hi-fidelity flight simulators, true to the aircraft? There are a lot of answers to that question, but one answer might be a realistic flight model that can reproduce aircraft performance, flight dynamics, handling qualities and control feel throughout the operational envelope. At Frasca, the Aeronautical Engineering team is responsible for making those things happen, and one of the invaluable capabilities that we rely on to that end is flight testing. By flight testing the aircraft we seek to replicate, we acquire the needed data to make the sim fly like the aircraft.
When thinking of flight testing, many people probably think of the efforts associated with new aircraft designs and the military or civilian requirements needed to prove out those new airframes. Expanding the performance envelope may come to mind, or validating predicted handling qualities and aircraft dynamics by performing a myriad of maneuvers and test points throughout the evolving flight envelope. Those examples are certainly core to the serious business of flight testing, and it is no secret that aircraft certification efforts can take years from start to finish before all test points have been flown, the data processed and analyzed, and any uncovered aircraft design issues have been addressed. So it may come as no surprise that the resulting data packages can only be purchased from the aircraft manufacturers at a steep premium, if at all.
Depending on the level of simulator qualification being sought, simulator flight models are actually required by government regulations to be validated against aircraft type-specific flight test data before they can be qualified for training, checking, and/or testing credits. Essentially, this means that simulator manufacturers have to prove that the simulator performance matches the real aircraft, and the only way to do that is to use flight test data.
With aircraft manufacturer data packages either being cost-prohibitive, tightly controlled, or otherwise unavailable, simulator manufactures must look elsewhere for this data. Sometimes outside flight test organizations can aide in collecting the data, but at Frasca, our preference is usually to collect these data packages ourselves. This gives us more flexibility and control over the process, which is important for us since the data packages often need to meet very high standards with respect to the methods & equipment used and the quality of data collected. Even if a simulator operator isn’t seeking a higher level of qualification that requires a high quality, type-specific data package, often there is still a strong case to be made, from a flight model development standpoint, for even a more basic flight test data package, collected using simpler methods and with less stringent requirements on the data.
When Frasca flight tests, regardless of the scope, there are always three main phases: Planning, Data Collection, and Post-processing & Analysis. These phases can be briefly summarized as follows:
- Planning: identify the target aircraft, scope of flight test, and create a detailed Flight Test Plan (FTP) that outlines the required data acquisition instrumentation and the tests and maneuvers to be flown.
- Data Collection: instrument the aircraft, coordinate with pilot(s) on fight and maneuver objectives, perform ground tests and shakeout flights, and then flight test aircraft covering at least the required minimum test cases, recording data during the entirety of each flight.
- Post-processing & Analysis: post-process and analyze the collected data; create a detailed Flight Test Report (FTR) that documents the entire effort and that can serve as a basis for simulator qualification as flight test validation data.
As one could imagine, in order to accomplish each of these phases a lot has to come together. We need the people with the training & expertise, which includes a team of flight test engineers and one or more pilots who know the aircraft (and in some cases are military flight test school graduates). We also need a flight mechanic to help out during the instrumentation phase, and even an FAA inspector will need to stop by to check things over and issue an experimental certificate before flight testing can commence.
Besides the people, we can’t flight test without the right tools & equipment. This of course starts with the aircraft we aim to flight test, which can sometimes be arranged with our customers, or may be arranged with 3rd party owner/operators. In terms of the equipment that Frasca engineers need to flight test, the list is extensive and covers not only hardware, but also a suite of software tools.
On the more sophisticated flight test campaigns, as much of the aircraft as possible is instrumented (always in a non-destructive manner). On the exterior, an air data boom and laser altimeter may be mounted, and position sensors could be installed on flight control surfaces. On the interior, the pilot’s flight controls are instrumented to record position and force data, and aircraft systems would be monitored & recorded, often by recording signals directly from the aircraft’s avionics suite. It is also crucial to have a video & audio record of the flight test, so this equipment will also be mounted in the cockpit to provide an overview of the instrument panel and pilot controls. All in all, it is a big job getting all the custom equipment designed and installed and can easily take months of preparation and typically a full week of aircraft downtime.
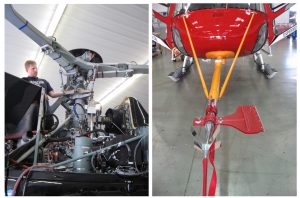
Left: Frasca Flight Test Engineer Chris Lyon inspects the rotor head assembly and rotor blade angle sensors on an Airbus Helicopters H125; Right: Air-Data Boom installed on an Airbus Helicopters AS350
Once all the sensors are installed on the flight test aircraft, we of course need a means to record the data. To this end a Frasca-designed data acquisition system and flight test engineer station are used. The engineer’s station includes a laptop computer networked with the data acquisition system to monitor aircraft systems and flight parameters in real-time and to control the recording equipment. The feature-rich software that runs on the flight test laptop is also designed by Frasca’s aeronautical engineers and affords maximum flexibility in terms of data recording, analysis, and test selection. One final note on installed equipment: some maneuvers can be quite challenging for pilots to fly well and in a repeatable manner. This is especially true for helicopter flight testing, so Frasca designed a special visual aid that is displayed so that pilots can monitor certain flight parameters in real-time. This real-time feedback to the pilot is invaluable to improve testing efficiency and data quality.
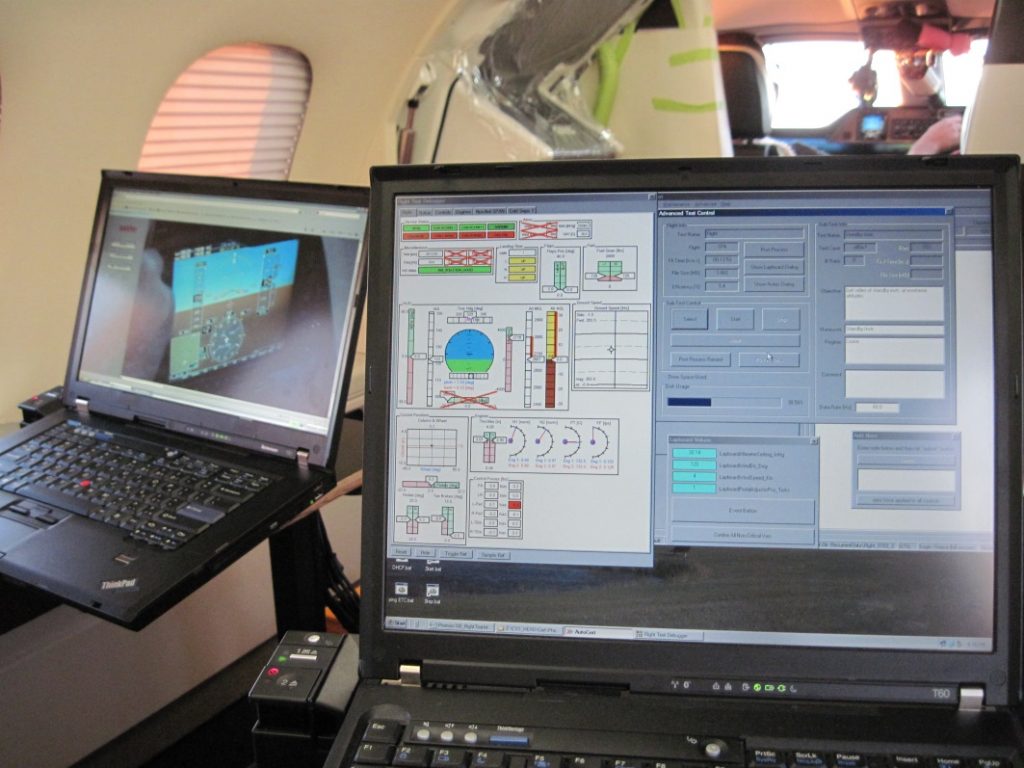
The flight test engineer’s station with laptops to monitor flight parameters, cockpit video, and to control aspects of data recording
As you can see, just getting ready to actually flight test can be a big job and requires a lot of team work. Once we’ve gotten to this stage, the flight test team will conduct one or more “shakedown” flights to identify any potential issues with the testing equipment. This is pretty important and usually uncovers something that needs to be addressed before we go about actually collecting data. Also, before we begin the in-air maneuvers, a series of hanger tests are completed to take baseline measurements and calibrate flight controls. Once that is done, the “up-and-away” flying can begin.
Once we are ready to begin the flying portion of a flight test campaign a series of daily pre-flight briefings will happen with flight test engineers and pilots discussing the goals and specifics of test maneuvers. Communication between the pilots and engineers is key–it has to be open and clearly audible in a sometimes noisy aircraft. An active back-and-forth between maneuvers is needed in order to provide feedback to pilots and engineers, alike.
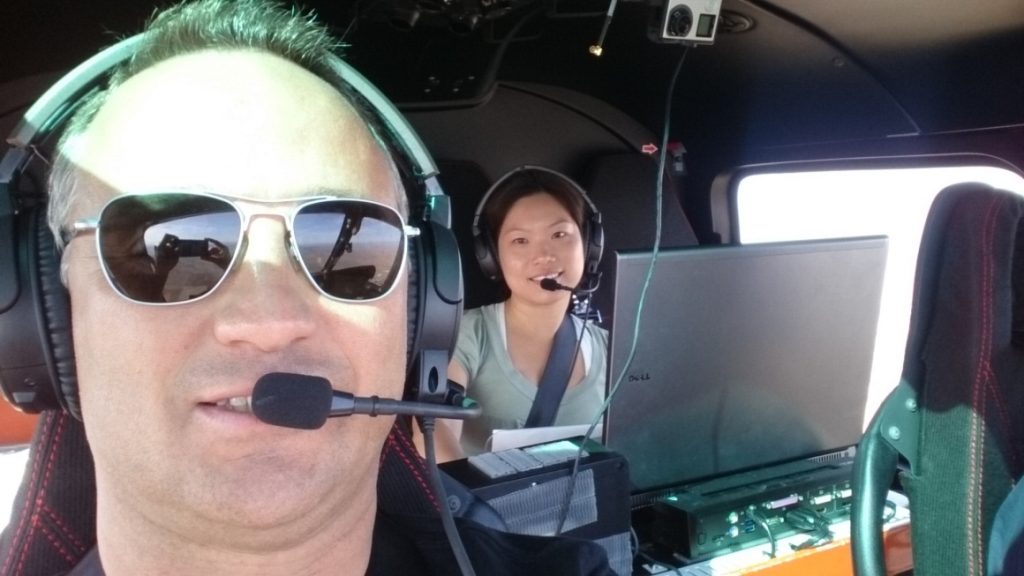
Flight Test Pilot Rucie Moore and Flight Test Engineer Bonnie Yam, taking a moment between maneuvers for a picture together.
It is worth pointing out that the flight testing done for the purpose of simulator model development and validation is not going to be nearly as extensive as that done for aircraft certification purposes. Potentially dangerous maneuvers or edge of the envelope flying that may be required for aircraft certification purposes are certainly avoided when Frasca flight tests. That’s not to say that it can’t get a bit exciting at times since we do, after all, need to collect data on all the main areas of aircraft performance and handling qualities. So there are certainly some maneuvers flown that are nothing like what a passenger would normally experience. Entry to autorotation in a helicopter, for example, can feel like you’re falling like a brick, and some maneuvers to test airplane handling qualities like roll response or rudder response tests can sometimes lead to short flights as some people onboard may need a break to let their stomachs settle. But we don’t need to push the envelope–the aircraft manufacturers have already done that, we just need to stay inside the envelope and fly the maneuvers in a safe manner.
This flying portion of flight testing is actually the shortest phase of the overall effort and is typically completed in 2-4 weeks depending on the aircraft complexity, scope of required data, and things out of our control like weather or aircraft maintenance issues that may arise. It’s a busy time though, usually with long days. At the conclusion of the flying, the aircraft will need to be returned to service–all the installed equipment needs to be removed and the aircraft returned to the operator exactly how it was received.
At this point, the Frasca team has usually collected hundreds of Gigabytes of data from aircraft sensors and cockpit video. In the following weeks and months, that data will go through an in-depth analysis, and it will be run through Frasca’s post-processing algorithms to split up test cases and apply a number of sophisticated post-processing techniques. At the end of this, engineers begin writing up the final Flight Test Report to document everything from start to finish: the flight test aircraft, the crew, the instrumentation, the data post-processing, and the test maneuvers that were flown. This report and the associated data package are then used as the Flight Test Validation Data for flight model development and simulator qualification.
All this time and effort–and the years of experience and expertise from Frasca’s engineers and the pilots we work with–it all goes towards Frasca’s goal to provide the best simulators available in the industry, to make better pilots, and to improve aviation safety.